Mantenimiento Predictivo y Preventivo. Clave para la Eficiencia Industrial
- 29 ago 2024
- 5 Min. de lectura
Actualizado: 29 oct 2024
En la industria de la automatización y manufactura, la eficiencia y la continuidad operativa son fundamentales para el éxito de cualquier empresa. Una de las mayores amenazas para estas metas es el tiempo de inactividad no planificado, que puede generar pérdidas económicas sustanciales. Según datos de Forbes, las grandes empresas manufactureras pierden anualmente alrededor de $1.4 billones debido a paradas no programadas, lo que representa un 11% de sus ingresos totales. Estos eventos no planificados son responsables de hasta el 92% de las interrupciones en la producción, con pérdidas que pueden alcanzar más de $300,000 por hora, y hasta $59 millones en sectores de industria pesada. Es evidente que el impacto financiero de estas interrupciones es devastador, lo que subraya la necesidad de adoptar estrategias proactivas de mantenimiento.

Mantenimiento Preventivo y Predictivo: Una Necesidad Imperativa
El mantenimiento preventivo y predictivo (PdM) se ha convertido en una herramienta crucial para mitigar los riesgos asociados con el tiempo de inactividad no planificado. El informe "The True Cost of Downtime 2024", publicado por Siemens, destaca que los costos asociados a las paradas no programadas han crecido exponencialmente en los últimos años, debido a la complejidad creciente de las cadenas de suministro y el aumento de los precios energéticos. En sectores como el automotriz, una hora de inactividad en una planta puede llegar a costar hasta $2.3 millones, lo que pone de relieve la urgencia de implementar medidas más efectivas de mantenimiento preventivo y predictivo.
La implementación de tecnologías PdM ha demostrado ser eficaz en la reducción significativa de las incidencias de inactividad. Las empresas que han integrado estrategias de mantenimiento predictivo han visto una disminución en el tiempo de inactividad mensual, pasando de 39 horas en 2019 a 27 horas en 2024. Estos programas no solo previenen fallos inesperados, sino que también optimizan la vida útil de los equipos, reduciendo los costos operativos a largo plazo y mejorando la eficiencia global de la planta.
La Revolución del IoT en el Mantenimiento Industrial
La introducción del Internet de las Cosas (IoT) ha transformado de manera radical cómo se lleva a cabo el mantenimiento en la industria, especialmente en sectores críticos como Oil & Gas y Energía. Los dispositivos IoT permiten la monitorización en tiempo real de los equipos, recopilando datos constantes sobre su rendimiento y estado. Esto posibilita no solo la identificación temprana de problemas, sino también la predicción de fallos antes de que ocurran, lo que es clave en el mantenimiento predictivo.

En el sector industrial, la integración de IoT se traduce en una mayor capacidad para tomar decisiones informadas basadas en datos, lo cual optimiza los tiempos de mantenimiento y reduce las paradas no planificadas. Para las industrias de Oil & Gas y Energía, donde el costo de la inactividad es especialmente alto, el IoT proporciona una ventaja competitiva significativa. Por ejemplo, sensores instalados en plataformas petrolíferas pueden monitorear la corrosión, la vibración de equipos críticos y las condiciones ambientales, permitiendo intervenir antes de que se produzcan fallas catastróficas.
Además, el IoT facilita una gestión avanzada de los repuestos. Los sistemas conectados pueden prever la necesidad de repuestos específicos, gestionando inventarios de manera proactiva y asegurando que las piezas críticas estén disponibles cuando se necesiten, reduciendo significativamente los tiempos de respuesta en caso de emergencias.
OEMs: Más Allá de los Manuales, Soluciones de Apoyo Especializadas
Para los fabricantes de equipos originales (OEMs), la relación con los usuarios finales no debe limitarse a la entrega de manuales y documentación técnica. En el mundo industrial actual, los OEMs tienen la oportunidad de agregar un valor significativo ofreciendo soluciones de apoyo al usuario final mediante planes de mantenimiento especializados. Estos planes deben ir más allá de lo básico, proporcionando asistencia técnica continua, formación, y herramientas digitales que faciliten el mantenimiento proactivo y predictivo.

El rol de los OEMs se está transformando hacia un modelo de soporte más integral, donde no solo se proveen equipos de alta calidad, sino también servicios que aseguran la optimización de su funcionamiento durante todo el ciclo de vida. Esto es especialmente relevante en industrias como Oil & Gas y Energía, donde los equipos operan en entornos extremadamente críticos y cualquier fallo puede tener consecuencias graves.
Los OEMs pueden ofrecer programas de mantenimiento personalizados que incluyen soporte técnico 24/7, monitoreo remoto mediante IoT, y plataformas digitales que permitan a los clientes gestionar el mantenimiento de sus equipos de manera más eficaz. Esta proactividad no solo aumenta la satisfacción del cliente, sino que también ayuda a construir relaciones más sólidas y de largo plazo, basadas en la confianza y el valor añadido.
Gestión y Control de Repuestos: Un Pilar Fundamental
Además de un mantenimiento efectivo, una buena gestión y control de repuestos es esencial para asegurar la continuidad operativa. En muchas ocasiones, la falta de piezas de repuesto críticas puede extender significativamente el tiempo de inactividad, incrementando las pérdidas económicas. Los estudios muestran que solo un 34.59 % del presupuesto de mantenimiento se dedica a mantenimiento correctivo, lo que subraya la necesidad de cambiar hacia enfoques preventivos y predictivos más robustos para evitar reparaciones costosas y pérdidas de producción no planificadas.
Una gestión adecuada de repuestos implica tener un inventario bien administrado y optimizado, que no solo incluya las piezas más críticas, sino que también esté alineado con las necesidades específicas de los equipos y las operaciones. Gracias al IoT, es posible implementar sistemas de gestión de repuestos más inteligentes, que rastrean el estado y la ubicación de los inventarios en tiempo real, optimizando la cadena de suministro y reduciendo los costos asociados a la gestión de inventarios.
La Digitalización del Mantenimiento en Oil & Gas y Energía
La digitalización del mantenimiento a través del IoT y otras tecnologías emergentes, como la inteligencia artificial y el machine learning, está redefiniendo el futuro del mantenimiento industrial en sectores clave como Oil & Gas y Energía. Estas tecnologías permiten no solo anticipar y prevenir fallos, sino también optimizar el rendimiento de los equipos y prolongar su vida útil de manera significativa.
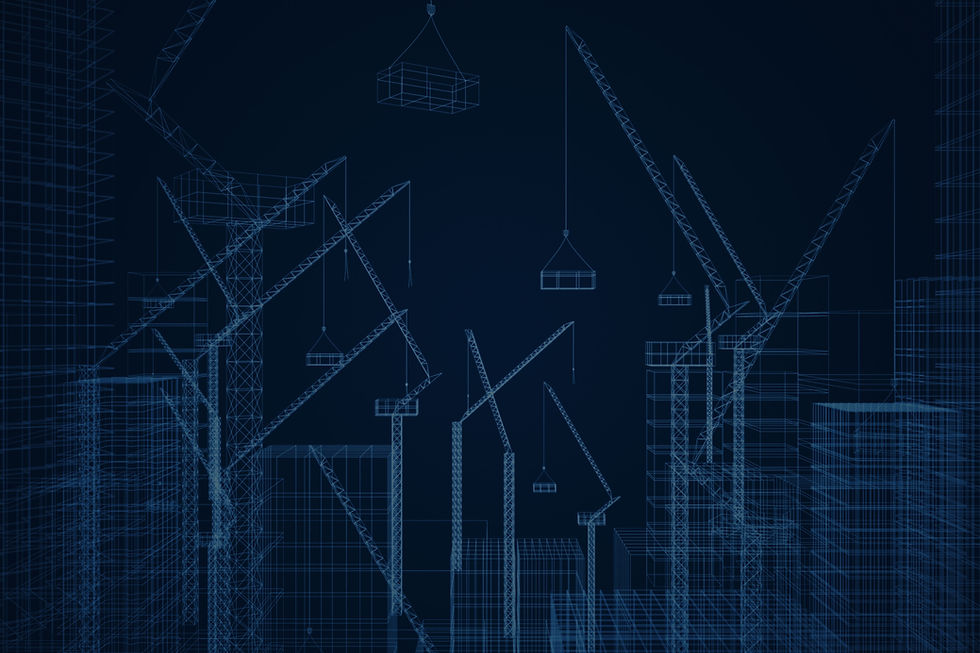
La implementación de soluciones digitales en estos sectores permite un enfoque más holístico y proactivo, gestionando activos con una precisión sin precedentes y adaptándose a las cambiantes necesidades del mercado energético. Esto no solo mejora la eficiencia operativa, sino que también contribuye a la sostenibilidad, reduciendo el consumo de recursos y minimizando el impacto ambiental de las operaciones.
Conclusión
La adopción de estrategias de mantenimiento preventivo y predictivo, impulsadas por la tecnología IoT y respaldadas por el apoyo especializado de los OEMs, junto con una gestión eficaz de los repuestos, es esencial para mitigar los riesgos de inactividad no planificada y mejorar la eficiencia operativa en la industria. Con la implementación de estas prácticas, especialmente en sectores como Oil & Gas y Energía, las empresas no solo pueden evitar pérdidas significativas, sino que también pueden optimizar sus operaciones y garantizar una mayor vida útil de sus equipos. La digitalización y la integración de tecnologías avanzadas marcan el camino hacia un futuro más eficiente y sostenible para la industria, y los OEMs juegan un papel crucial en guiar a sus clientes en este viaje hacia la excelencia operativa.
Comments